Do you know anyone who might be interested?
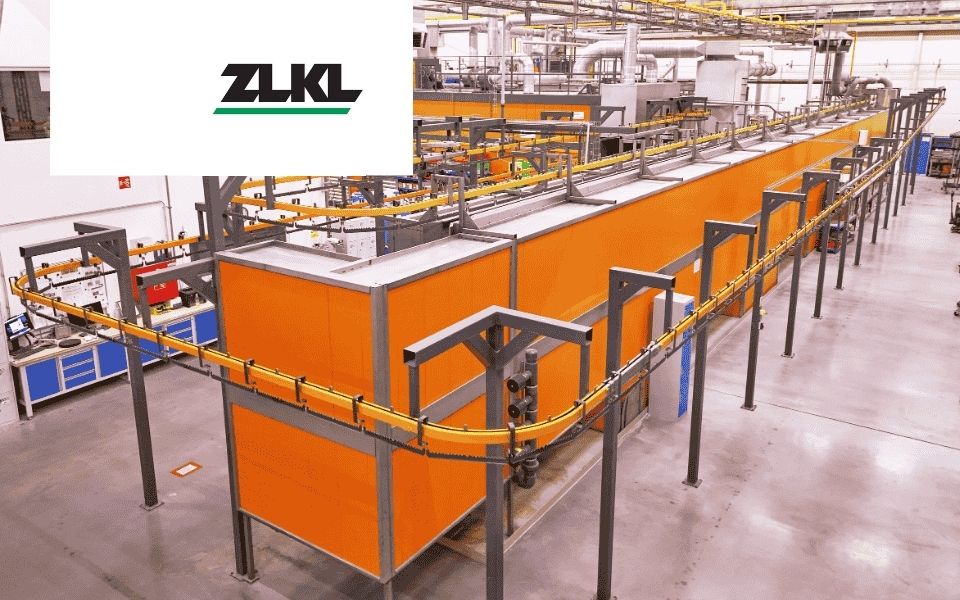
The specifics of this implementation were the requirement for multi-metallic chemical pre-treatment with the maximum possible level of automation. Therefore, we designed a 5° chemical pretreatment with automatic pressure control on the sprayers with automatic chemical dosing. The high level of automation is confirmed not only by the robotic paint booth, but also by our HiVision® central control system.
Customer | GAF s.r.o. |
Year of Realization | 2024 |
Location | Žamberk (CZ) |
Industry | Job coating |
Flow profile | 1000 mm x 1800 mm x 3000 mm (wxhxd) |
Technology |
|
In the case of oversized products that do not fit the passage profile of the automatic line, we added a Wash Box with bath recycling to our paint shop. Each of our paint booths is designed with the environment in mind, so we integrate bath recycling. For the heating of the active bath, we have supplemented the technology with electric boilers with a total output of 120 kW, which are connected to solar panels with an output of up to 400 kW. Based on a signal from the operator, they will replace gas heating.
For reasons of space, the neutralization station is located on a steel platform above the coating line.
The HiVision® control system doesn´t take care about recipes only, but also monitors the colour change in the painting booth.
The entire implementation up to commissioning took place within 2.5 months.
Show more information - Coating facilities
View productDo you know anyone who might be interested?