Do you know anyone who might be interested?
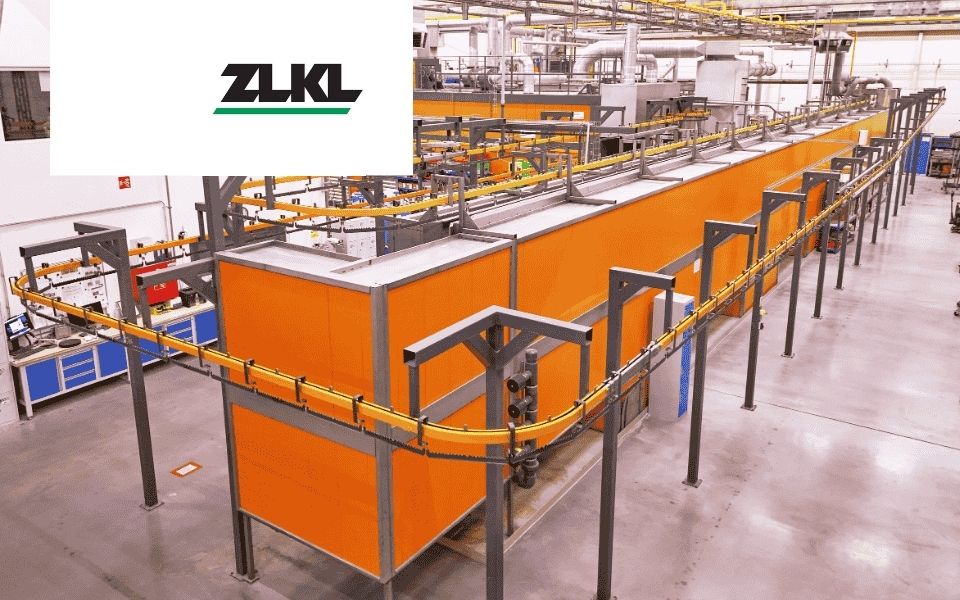
For Vaillant Group, we have implemented a complex fully automatic painting line for the processing of sheet metal parts for heat pumps. This modern technological complex covers an area of 10,000 m² divided between two halls.
Customer | VAILLANT GROUP Heat Pump Production s.r.o. |
Year of Realization | 2023 |
Location | Senica (SK) |
Industry | heat pump production |
Flow profile | 1900x2600x400mm (h x l x w) |
Technology |
|
The first hall, measuring 6,000 m², is used for the actual painting process, while the second hall, measuring 4,000 m², is used to distribute the finished products to eleven downhanging stations. Each segment of this facility has been designed with redundancy and efficiency in mind, which is reflected in the dual design of the key components: two chemical pretreatment ovens, two drying ovens, two painting booths and two curing ovens.
Our technology was designed for a challenging customer who required a system capable of painting up to 300,000 heat pumps per year. The system incorporates a fully automated waste water recovery process with vacuum evaporation, which significantly reduces water consumption.
The main component is a conveyor system of more than 3,370 metres with 25 drives, which ensures the smooth transfer of products through the paint line. The products are distributed on four types of hanging traverses by means of three hanging stations with two levels. The overall process is completed at eleven down hanging stations.
Ensuring that each product is correctly hung and arrives at the appropriate hanging station is crucial to the efficiency of the entire process. To this end, we have programmed the HiVison® control system, which is linked directly to the ordering system and thus optimises the entire production flow, including the placement of parts on the individual trolleys. This guarantees the highest possible capacity of the paint line and reduces the possibility of error.
Show more information - Coating facilities
View productDo you know anyone who might be interested?