Do you know anyone who might be interested?
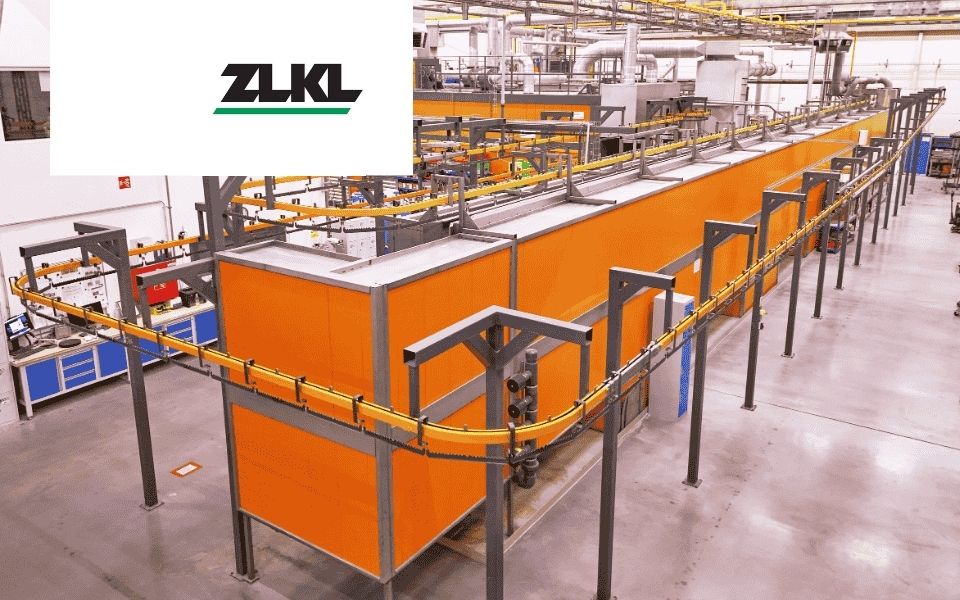
In order to increase efficiency and productivity, the old manual paint booth was replaced with a new, fully automatic paint booth for rapid colour changes with Sames application technology. The technology also includes our innovative ITS powder centre. In addition, the control of the entire technology has been integrated into a new control system.
Customer | ZK DESIGN a.s. |
Year of Realization | 2022 |
Location | Velká Polom (CZ) |
Flow profile | 1500 x 800 x 2500 mm (h x w x l) |
Industry | Production of shelving systems, office equipment |
Technology |
|
The paint booth is equipped with new two-axis manipulators Inorecip, which are equipped with 6pcs of automatic guns of new generation Inogun A FCC. Product detection is ensured by an optical gate located in close proximity to the booth. The manual painting platforms on each side of the booth are extracted separately, directly into the end filter to avoid excessive paint contamination.
An innovative ITS powder center delivers powder to the spray guns, exhausts fumes, controls the ejector blocks and cleans the powder hoses. The entire process, including the return of powder paint from the cyclone, is controlled automatically.
An end filter with an exhaust capacity of 16,000 m3/h provides sufficient exhaust power and, thanks to the €Saver-like superstructure, we are able to use the power more efficiently and, above all, to reduce energy consumption.
As part of the implementation, the existing technology was also intervened. This has been completely integrated into the new control system, which brings many benefits to the investor. First of all, the lifetime of the technology is extended and thus its reliability is increased. In addition, the control via the new 24" Full HD graphic terminal provides a much better overview of the entire technology. The ability to connect to the terminal via a web interface using the WebControl module is standard.
The €Saver system installed on the painting booth as well as the chemical pre-treatment technology helps to minimize power consumption. The painting booth suction filter alone offers energy savings of up to 30%.
Show more information - Coating facilities
View productDo you know anyone who might be interested?