Kennen Sie jemanden, der Interesse haben könnte? Zögern Sie nicht und teilen Sie!
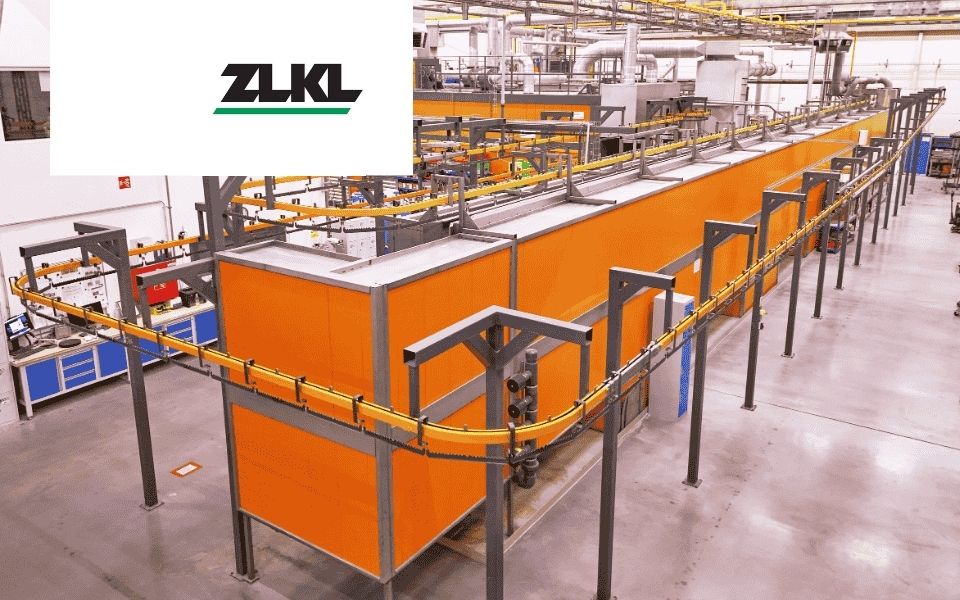
Die hohen Anforderungen der Endkunden zu erfüllen, ist immer sehr anspruchsvoll, insbesondere im Automobil- und Fertigungsbereich für Unternehmen wie Volvo, Claas oder Caterpilar. Bei der Umsetzung eines außergewöhnlichen Projekts mit vielen innovativen Elementen nach Konzept Industrie 4.0 war das nicht anders.
Jahr der Realisierung | 2020 |
Lokalität | Čadca (SK) |
Durchgangsprofil | 800 x 1400 x 2500 mm (b x h x l) |
Technologie |
|
Die geforderten Parameter an die Anlagenkapazität von 3 Minuten/Trolley in allen Betriebsarten und für die Pulverbeschichtung 90 Sek./Trolley waren eine echte Herausforderung. Konzipiert wurde die Anlage als Kombianlage mit einer 20-stufigen Oberflächenvorbehandlung auf Basis von Zn-Phosphatierung in der Tauchvariante, gefolgt von einem KTL-Knoten zum Auftragen der Grundierung. Die vollautomatische Übergabe vom Tauchbereich an das Power & Free-Fördersystem leitet das Material anschließend weiter zum Trockenofen. Ausreichende Anzahl von Positionen bilden einen Puffer vor einem speziellen Knoten zur Verteilung der durch das Tauchbecken parallel laufenden Trolleys, die nacheinander den Lackierbereich der Anlage durchlaufen. Hier kann eine Taktrate von bis zu 90 Sek./Trolley erreicht werden. Die Schnellfarbwechselkabine von Sames sowie andere Anlagenteile ist mit einer Vollautomatik zum Laden von Produktrezepturen über das SAP ERP-System ausgestattet.
Für die Belieferung des Pulverbeschichtungszentrums sorgt der mobile Roboter, der bedienerlos die Farbe aus dem Lager holt und gleichzeitig ihr genaues Abwiegen durchführt. Das Gewicht der verbrauchten Farbe wird im System genau erfasst und im Produktionsauftrag zur weiteren Kalkulation und Berechnung der Lackiereffizienz gespeichert.
Hinter der Lackierkabine selbst verbirgt sich ein weiterer innovativer Teil der gesamten Technologie, nämlich ein völlig neues und einzigartiges System zur berührungslosen Robotermessung von ungebrannter Farbe HiVision DeepControl. Das Roboterpaar misst nicht nur präzise die Farbendicke mit einer Genauigkeit von +/- 5 µm, sondern speichert auch alle Parameter der Produkte in einer Datenbank. Eine automatische Korrektur des Sprühsystems bei Unter-/Überschreitung von Grenzwerten ist ebenfalls zwingend erforderlich. Alles findet während des Vollbetriebs der Lackiererei statt. Dieses interaktive System sorgt für eine deutliche Reduzierung des Verbrauchs von Pulverfarben in der Größenordnung von mehreren zehn Prozent, reduziert den Ausschuss und trägt damit maßgeblich zur Einhaltung von Lieferterminen bei. Die finanziellen Einsparungen können je nach Betriebsgröße bis zu mehreren Millionen Euro pro Jahr betragen.
Alle Technologien sind streng nach den BREF-Richtlinien konzipiert, die den Einsatz der besten bekannten Technologien/Prinzipien (BVT) hinsichtlich der Betriebsökologie vorschreiben.
Im Anschluss an die Spritzkabine erfolgt das Brennen in einem konventionellen Gasofen, sowie nach der KTL-Lackierung in einem Trockenofen. Beide Öfen sind mit ökologischen Aggregaten mit Direktbeheizung und emissionsarmen Gasbrennern ausgestattet. Das Abwasser wird vollautomatisch entsorgt. Eine kontinuierliche Aufzeichnung der Leistungsparameter am Ausgang unter
Das Power & Free Fördersystem ist ein wichtiges Element der gesamten Anlage und gewährleistet den Transport von Produkten bis 400 kg/Trolley mit einer Geschwindigkeit von max. 3 Minuten. Es ist mit automatischen Weichen, Stationen zum Aufhängen und Abhängen, Umhängesystem ausgestattet und ermöglicht den Transport von Produkten bis 800 x 1400 x 2500 mm.
Komplette Rezepturen und der Arbeitsvorrat werden aus dem ERP-System des Unternehmens in eine SQL-Datenbank geladen, die zum Datenaustausch mit der Anlage dient. Ebenso werden die technologischen Daten, wie beispielsweise die gemessene Farbschichtdicke, in eine Datenbank zur Nutzung im ERP eingepflegt. Dabei handelt es sich nicht um ein einfaches Kommunikationssystem, sondern um ein sogenanntes Big-Data-Verfahren. Der Zugriff auf die Steuerung erfolgt nicht nur lokal, sondern ganz einfach über die Cloud-Schnittstelle von jedem PC- oder Mobilgerät. Zubehör und Peripherie wie Neutralisationsstation, Lüftungsgerät, Heizraum, VE-Wasser-Erzeugung oder Backup-Aggregate bilden eine separate Einheit, die sich dank integrierter HiVision-Module einfach steuern und in ihrem Betrieb effizient auswerten lässt.
Das Projekt wurde in einer Rekordzeit von 3 Monaten umgesetzt und zum vereinbarten Termin in Betrieb genommen und zählt eindeutig zu den technologisch fortschrittlichsten Technologien in diesem Bereich.
Mehr Infos anzeigen - Lackieranlagen
Produkt anzeigenKennen Sie jemanden, der Interesse haben könnte? Zögern Sie nicht und teilen Sie!